American Airlines plane forced to land 250 miles into flight due to crack in windshield
It comes after a door panel blew off during an Alaska Airlines flight in January
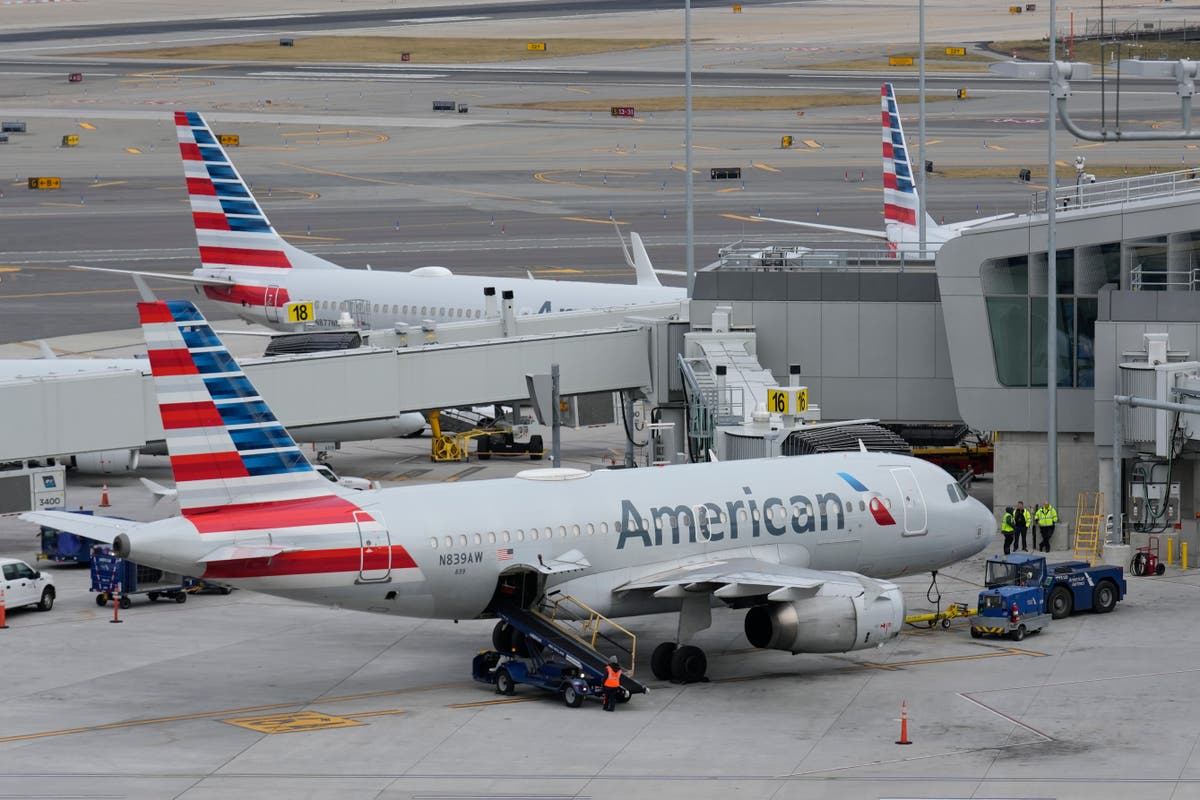
Sign up to Simon Calder’s free travel email for expert advice and money-saving discounts
Get Simon Calder’s Travel email
American Airlines passengers were left stuck in Boston after their flight was forced to land just 250 miles into its journey after a crack was discovered in the windshield.
The flight, which was on its way to Spain, was 250 miles from the coast of Massachusetts over the Atlantic Ocean when it was forced to divert.
Massachusetts State Police said flight 94, a Boeing 777, was less than two hours into the journey after taking off from New York City‘s JFK Airport at 7:28pm, when an Alert 2 emergency was declared due to a crack in the windshield in the cockpit.
An Alert 2 is declared when the flight is experiencing “major difficulties” or when a “difficult or crash landing may be expected”, according to the Federal Aviation Administration.
The flight landed safely at 10:14pm at Logan International Airport, according to the airline, who said in a statement that the diversion was down to a “maintenance issue”.
The aircraft was taken for an inspection by American Airlines crew. No one was hurt in the incident.
The airline said passengers will be taken to Madrid on a replacement jet on Thursday afternoon.
The carrier said in a statement: “The flight landed safely and the aircraft was taken out of service to be inspected by our maintenance team. Customers will re-depart for [Madrid] tomorrow on a replacement aircraft. We never want to disrupt our customers’ travel plans and apologize for the inconvenience this has caused.”
In a separate statement on X, the airline said: “Safety is always at the top of our list! Delays are never an easy decision but sometimes are needed to ensure the safety of everyone on board.”
Following the emergency landing, passengers were told they would be put up in hotel rooms overnight and receive food vouchers, according to airline reps.
Some passengers were left frustrated, however. “How does a multi-millionaire company with so many resources not foresee this,” passenger Nico Moreno told WBZ after getting off the flight.
“The type of solution they give you is very minimal in terms of, you don’t make up for the money I lose when I miss my job. You don’t make up the time I lose for everything I have at home, all the situations, no? ”
Boeing has been under scrutiny since a door panel on a different kind of aircraft, a 737 Max 9, blew off during an Alaska Airlines flight in January.
Several passengers on board were injured in the incident, which grounded all Boeing 737 Max 9s and prompted investigations by the Federal Aviation Administration (FAA) and the National Transportation Safety Board, into the aircraft manufacturer and Spirit AeroSystems, which made the doorplug.
Reports released since have suggested the plane did not have the critical bolts it needed to keep the doorplug in place when it left the factory.
Following the incident, Alaska Airlines and United Airlines, which operate 79 of the planes, said they, too, found loose bolts on some of their aircrafts.
Earlier this month, the head of the FAA pledged to use more people to monitor aircraft manufacturing and hold Boeing accountable for any safety rule violations.
This week the FAA said it is giving Boeing 90 days to come up with a plan to fix quality problems and meet safety standards.
“Boeing must commit to real and profound improvements,” said FAA Administrator Mike Whitaker. “Making foundational change will require a sustained effort from Boeing’s leadership, and we are going to hold them accountable every step of the way.”
Boeing CEO David Calhoun has said that the company “will develop the comprehensive action plan with measurable criteria that demonstrates the profound change that Administrator Whitaker and the FAA demand”.