How To Increase Manufacturing Efficiency Without Compromising On Quality
Improve manufacturing efficiency without laying off staff or replacing with ineffective materials. We hope to help those struggling with this balancing act.
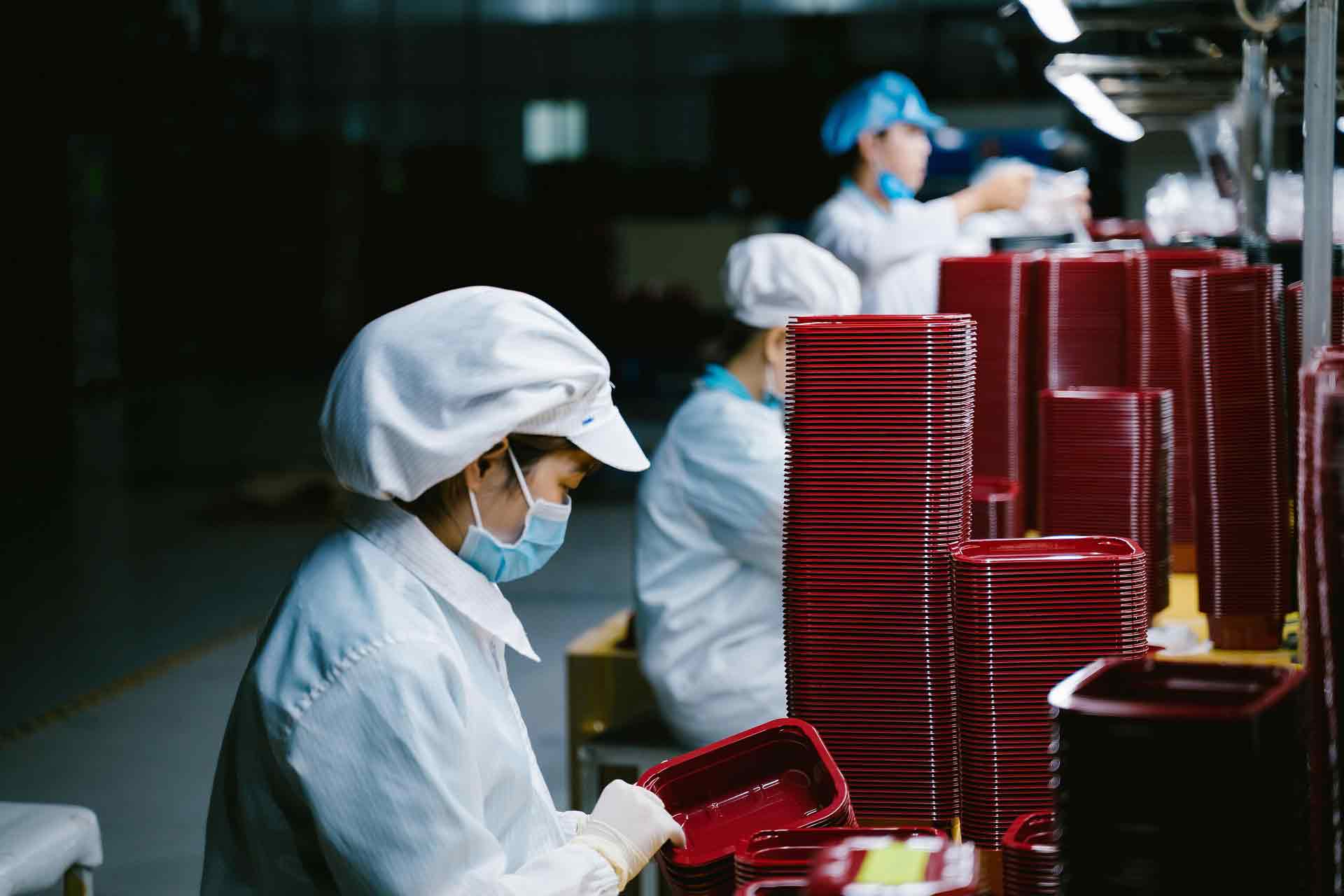
If you’re trying to produce more in the same period of time with the same resources, there are chances that the quality of the product may deteriorate. Here are some tips and tweaks that you can implement at your factory to increase the manufacturing efficiency while making sure you do not compromise on the quality of the products. ~ Ed.
The manufacturing process itself takes time to manufacture if you really think about it. Every element is as complex as the moving parts in any machine, and while all systems can use improvement, messing with a certain element and failing to consider the wider context it operates in can cause problems. We can’t just take the fan belt out of a car or replace it with an inappropriate substitute and expect the same performance from such a vehicle.
The same logic can apply to your approach to optimizing your efficiency. “If it isn’t broke, don’t fix it” can sometimes leave out the possibility for repairs that genuinely work, but the principle isn’t a bad one.
In this post, we hope to help those struggling with this balancing act. After all, passing on the cost of savings in production can help, but if you’re unable to sustain the same quality as before, the process isn’t worth it. We hope the advice we give can reverse that direction.
7 Ways to Increase Manufacturing Efficiency Retaining Quality Standards
Here are the tips and tweaks from the experienced and the experts to help you make more money.
Perfect Your Storage Cycle
It may seem that storage is part of the process that comes well after you’ve manufactured something, and that raw materials need little in the way of sophisticated planning outside of being safely present, easy to access, and secure. But of course, that’s not always the case.
That’s because storage layout directly impacts every aspect of production time and quality. For example, materials that sit in the wrong conditions or stay on shelves too long can degrade quite easily, which eats into the discount of your bulk purchase.
It’s also pretty obvious that poor organization will make you suffer unnecessary delays. Investing all you can in a well-planned storage system is wise, because it keeps materials close to their point of use, rotates stock effectively, and also ensures proper environmental conditions for sensitive items.
You might benefit from implementing a more thoughtful reorganization of your storage areas and as such limit hours of wasted movement and searching time. So perhaps it’s not your factory line that needs the upgrade, it’s your warehouse, your storing facilities, and your loading bays. A new indexed or barcode scanning system might be best, or investing in new storage movements facilities like a new fleet of forklifts or conveyors could help. Perhaps you just need to hire a warehouse manager, who could pay for their own salary tenfold each year in improved efficiency.
Frequent, Scheduled Maintenance
Maintenance goes far beyond routine cleaning and basic upkeep. Each piece of equipment needs specific attention, such as monitoring belt tensions and gear alignments. Machine operators, if you train them well, become skilled at noticing subtle changes in equipment performance through sound and vibration.
This awareness, combined with regular professional maintenance, keeps production running smoothly and equipment lasting longer. It’s essential that you implement a healthy documentation of maintenance activities to give the entire management team data about equipment performance.
Maximum Capacity Measures
Ultimately, every production outfit, no matter how large or sprawling or impressive, will have production capacities. This is especially strained during seasonal periods of course, but still worth keeping in mind.
It’s important for managers and business owners to understand that while machines might technically handle higher volumes, human operators and material storage limitations often set the real maximum capacity, and it’s important not to push these constraints but invest in a wider operation if you hope to achieve more.
After all, running equipment at its absolute limit will almost certainly cause increased downtime and quality issues. Production targets based on actual operational capacity, rather than theoretical maximums, even if you have to renegotiate deadlines with your clients, will help with consistent output and better product quality. A good investment is to have regular analysis of capacity usage patterns, because then you can see where additions or alterations to your production timeline are possible.
It also means avoiding overbooking yourself and struggling to meet the demands of multiple clients, which will almost always cause disappointment if you’re not careful and disciplined enough to avoid it.
Offloading Waste/Scrap
Good waste management is usually a worthwhile practice to invest in for obvious reasons. But if your business deals with valuable materials or those that may hold value or purpose beyond your own uses, optimized or sustainable waste management alters what could be a pure cost center into a potential value stream. To start with, you’ll have to integrate proper sorting and handling of recyclable materials, which opens up additional revenue if you can find a worthwhile sale. This isn’t as difficult as you may imagine give creative reuse of manufacturing byproducts.
For example, unused biofuel and scrap metal could provide two options. At the very least you might work with sustainable partners to help reduce the impact of your wastage, which could possibly help you make use of more recycled output once again.
Private Safety Audits
Instead of bringing in outside consultants who might not understand your specific setup, running your own regular safety reviews makes a lot of sense, as long as they can be conducted by another part of your department who will be utterly stringent.
Walking through your facility with fresh eyes every month or so will spot issues you might normally avoid. Of course, it is worth investing in a private auditor too if you think that you may be too biased, or if you have huge inspections coming up and you want to meet even more stringent standards before they come.
A great approach is to include your floor workers in these reviews because they’re the ones who know exactly where things could be safer or work better. Moreover, when such staff see their suggestions being taken seriously, they’re much more likely to speak up about other improvements in the future and not sweep their difficulties under the rug at all.
Custom Machinery
A manufacturing line might have been curated thus far with standard machines purchased from catalogs and integrated as part of a logical line. That’s perfectly normal of course, as every manufacturing setup is different and some modularity is important. It’s not like you’re going to invent every machine you need yourself to begin with either, as most practical purposes have already been made available and sold at scale, allowing you to enjoy some of those savings.
However, a simple adjustment to a conveyor system or a modified attachment might solve your problem without requiring a fully custom unit. A high-quality set of precision bearings could be a worthwhile investment for custom machinery, allowing you to gain further functionality over time. Incremental improvements like that can add up to a setup that’s perfectly fitting to your needs.
Supplier Alternatives
Nobody likes to think about their suppliers letting them down, but it happens. Sometimes it happens often if there are shortages or if a strange little quasi-trade war is taking place (and unfortunately, in today’s political reality, this is unlikely to be that infrequent).
Having a backup plan doesn’t mean you don’t trust your main suppliers, of course, as it’s just good business sense. Building relationships with two or three reliable suppliers for your essential materials can save you massive troubles down the line where you scramble to put those in at the time. You may pay touch more sometimes, but that’s better than having your whole production line grind to a halt because of a delayed delivery. If you host frequent chats with your suppliers for reviews it can also help you spot potential issues early and often lead to better service overall.
Wrapping Up
Perfecting your storage cycle, scheduling frequent maintenance, measuring the maximum capacity, offloading the waste, conducting private safety audits, customizing your machinery, and building relationships with alternative suppliers.
With this advice, we’re certain you’ll be able to continue improving manufacturing efficiency without laying off staff or replacing with ineffective material replacements.
Over to you
If you have a manufacturing facility, what measures do you take to produce more in the same duration keeping the quality standards? Share your tips and experiences in the comments below.
Disclaimer: Though the views expressed are of the author’s own, this article has been checked for its authenticity of information and resource links provided for a better and deeper understanding of the subject matter. However, you're suggested to make your diligent research and consult subject experts to decide what is best for you. If you spot any factual errors, spelling, or grammatical mistakes in the article, please report at [email protected]. Thanks.